When selecting a cutting tool that can withstand high temperatures, several different criteria must be carefully evaluated, but one of the most important deciding factors that one should be well aware of is the metal melting point itself.
“Can such cutting tools withstand temperature as high as the metals we’re manufacturing?"
“Which cutting tools should be recommended for which types of metals?"
Or "Should we use the same cutting tools for all types of metals?"
In this article, we will summarize common melting points for ferrous and non-ferrous metals as well as the relationship between the cutting tools and melting points. Hence, you could figure out how powerful cutting tools with high melting temperatures could enable faster manufacturing and reduce excessive materials.

About Melting Point
We see the phenomenon of melting every single day and feel like “melting point" term is super familiar but have you ever imagined what it really looks like and how it impacts the entire manufacturing process?
“Melting", or fusion, means a change of physical state in a substance turning from solid to liquid with the participation of heat during the process. And the temperature at which a solid transforms into a liquid is simply called “melting point".
In the manufacturing process, once the heat is added to metals and melting point is achieved, metals will start to be deformed and its original shape will be no longer preserved. We can see this phenomenon clearly in the thermal cutting phase or pre-treatment of scrap.
Depending on the alloy composition, melting point can fluctuate from the lowest temperature (like Mercury with -39oC (-38oF)) to the highest temperature (Tungsten with 3,400oC (6,150oF)).
But when determining the correct melting point for metal products, one thing that's worth considering here.
What's the difference between degree Celsius and degree Fahrenheit?
To avoid serious mistakes caused by misinterpretation that we might probably face when we've got too much on our plate at work, let's distinguish the difference between degree Celsius (oC) and degree Fahrenheit (oF) first.
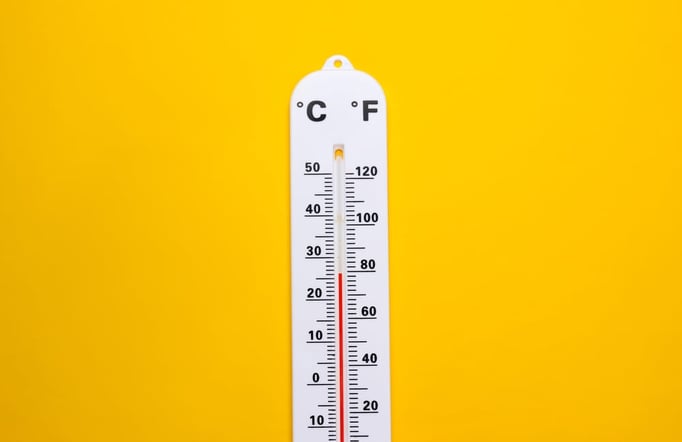
Degree Celsius (oC) and degree Fahrenheit (oF) are both units of temperature.
We can convert degree Celsius into degree Fahrenheit just by using below formula.
Temperature Conversion Formula (oC to oF)
(0°C × 9 ÷ 5) + 32 = 32°F
For example: What is the equivalent of 1,000oC in oF?
We guess that you got the answer right there!
Yes, it will be (1,000oC x 9 ÷ 5) + 32 = 1,832oF, quite easy, right?
In addition to the temperature conversion formula, the difference between oC and oF also lies in the fact that while almost more than 90% of countries using degree Celsius (oC), few nations such as the United States, the Bahamas, and the Cayman Islands still adopt degree Fahrenheit (oF) as their official unit of temperature.
The thing is, don't forget to check exactly which unit of temperature that your business partner is using in any phases of the transaction. For example: If melting point in the required technical specification shown as 1,000 degree, make sure that it's 1,000 degree Celsius (oC) or 1,000 degree Fahrenheit (oF), not something in between.
We now understand the definition of melting point and what factors to consider when determining melting point for metal products. Let's go over the main different types of metals in the following section, as well as learn how to lower melting point for each type.
Main Types of Metals
There are many ways to classify types of metals but in this article, we divide metals into 2 main types: ferrous metals and non-ferrous metals.
Ferrous metals refer to any metal that is primarily comprised of iron and have magnetic properties like steel or cast iron.
Ferrous metals make up of almost 90% of worldwide annual production and play a huge role in housing construction and industrial fabrication.
Non-ferrous metals, on the other hand, refer to metals without the composition of iron like aluminum, copper, tin, lead, or zinc.
Due to its lightweight properties, scarcity and expensiveness, non-ferrous metals are often used extensively in the automotive, aerospace or high-end luxury furniture industry where cost element is not a big deal to the end-users.
Melting Point of Ferrous Metals
Steel and cast iron are the two most important components in the recycling process to make new products from steel scraps. Their melting points are usually above 1,000oC (1,832oF). This high temperature is a real exhaustion for the engineers to dissolve metals into solutions from the original shape during the smelting or scrap cutting process.
Because, the higher the temperature becomes, the more heat is needed to melt the metals.
So, in what ways could we lower the melting point of ferrous metals?
Indeed, we could reduce the melting point to a lower level than its actual temperature by adding more carbon to steel or cast iron. This practice can save us from using excessive materials because a smaller energy consumption will be required during the smelting or scrap cutting phase as a result.
Take a quick look at the table below for the actual melting point of ferrous metals.
(Table of Melting Point for Ferrous Metals in Cesius and Fahrenheit scale)
Melting Point of Non-ferrous Metals
When it comes to lowering melting points for a more efficient manufacturing process, the same recipe applies to non-ferrous metals. For example, instead of carbon, we can add lead to tin or tin to lead in order to decrease the rich components that each non-ferrous metal contain.
In the table below, it is noticeable that melting point of non-ferrous metals can be higher or lower than 1,000oC (1,832oF) which gives us an impression that melting point of ferrous metals are higher than non-ferrous metals in general, but is it true in all situations?
Do ferrous metals have higher melting point than non-ferrous metals?
The answer is "Not exactly so!". Sometimes, melting point of ferrous metals is higher than non-ferrous metals and vice versa. And below table is only a summary of frequently used non-ferrous metals, not all. If you still have more questions in regard to melting point so that you could choose the right cutting tool, click here to get in touch with Daiwa Lance technical support team!
(Table of Melting Point for Non-ferrous Metals in Cesius and Fahrenheit scale)
Why Melting Point Matters So Much in Metal Cutting?
The high melting point is a stumbling block when selecting suitable cutting tools for metal products. Even if we have a million reasons to select cutting tools based on their impressive products offerings such as great wear, excellent corrosion-resistance, more-than-reasonable price or the sweet promise of gaining a stunning long-lasting structure, a mismatch between metal melting point and the high-temperature tolerance of cutting tools can still ruin everything.
In order not to incur loss when buying cutting tools, remember to sharpen your knowledge of metal characteristics, always have the melting point summary at your hands, and most importantly, choose cutting tools with heat-resistant tolerance higher than the temperature of metal melting point itself in a wise way.
Looking for more relevant information on this topic? Read our article that introduces the cutting tool that can generate a temperature up to 4,000oC (7,232oF) or subscribe here to gain more insight of the steel and metal industry from Daiwa Lance's weekly blog!
- Category:
- Daiwa Lance Products
- Keyword:
- SDGs
- Oxygen Lance
- Thermic Lance